Dean's 1923 custom T-bucket PROJECT
Dean started with the basic plan to build a hot rod that would be "the perfect car to have", but no real specific details beyond that. The thought that this may be the only rod he'd ever build also influenced the decision making, and created something of a 'no compromise' attitude.
The first step in what turned out to be a seven-year build was the purchase of a $200 fibreglass t-bucket body. At that stage, Dean thought if the idea didn't really go anywhere, he wouldn't be too out-of-pocket. As it turned out, that fibreglass body proved to be one of the project's least expensive components! A big turbo was in the mix early, too, which steered the project toward Japanese power. A wrecked Nissan 300ZX would provide the engine and gearbox, but to look at the finished project, you wouldn't pick there's a VG30DETT V6 under all those braided lines and mandrel-bent custom pipework. And as for that big turbo, Dean chose a Garrett GT42R, which is probably closer to truck than car-spec, and provides this custom rod with awesome grunt.
Dean's mechanical knowledge and background in fabrication - on everything from kids' bikes to tow trucks - made the bespoke requirements of many of the project's components a little easier, but this build was still very much a case of trial and error: thinking about things, testing them, then rethinking them if they didn't work out. For example, Dean wanted the traditional T-bucket's vertical steering wheel, but making that steering work with the engine, transmission, front end and chassis configuration would have been extremely difficult, so that idea was abandoned.
The chassis was completely scratch-built, with an interesting 'two layer' system using 4x2 section rectangular tubing for the top rails and 2x2 for the lower rails, with trellis-style bracing in between. This served two purposes. The weight helped keep the turbo V6 under control, while ensuring overall strength, as sections of the upper rails had to be cut to fit in the engine componentry. The upper and lower rails also proved to be ideal for mounting the front suspension's upper and lower A arms, which were also custom built.
That front suspension proved to be one of the project's turning points. Dean had built his own front suspension, but was informed it wouldn't pass inspection for roadworthy. Resisting temptation to abandon the project, Dean instead turned to his good friend, Pat, who also happened to own Racecraft Engineering at the time. Pat told Dean he could build a custom front suspension using stainless steel tubing that would pass inspection easily. The 'but' with this was that while Pat could build it, it was going to cost plenty in materials alone, without factoring in his time. Sticking to his original credo of using the best parts possible, Dean bit the bullet, designing the front suspension which Pat then fabricated and had signed off by an engineer. With that hurdle behind him, Dean was back on track.
With the chassis and suspension sorted, Dean finished off the engine, adding a Greddy boost controller to the big Garrett GT42R, twin 48 mm wastegates, 1000cc injectors, GFB blow-off valve, an Autronic SM4 computer, R500 CDi ignition, chromoly fly wheel, twin plate Nismo clutch, XRP oil filter and more. That last component is a good example of the meticulous approach Dean took to this project. Dean had originally fitted a standard Earls oil filter, but was getting discrepancies in oil pressure from the two gauges he was running - one in the block, and the other at the pump. Removing that filter equalised the pressure, but reduced it, so Dean fitted the non-restrictive, race spec XRP filter, which cured the problem.
On first inspection of Dean's project, you can't help but notice the abundance of braided lines and anodised joiners and elbows, not only through the engine bay, but for the wiring and just about every bit of tubing as well! Dean told us he started with some braided hoses for the radiator only, and it just grew from there. When the project was completed, Dean did a count and there are no fewer than 225 hose connectors used, and more than $14,000 spent on these and the braided lines. He did put the brakes on at that point - saying that if he continued to spend money on trinkets, he'd never get the project finished!
There's a bunch of custom made stainless steel parts in the build, too, not least of which are the valve covers, inlet manifold, fuel and oil tanks. These were designed and all hand fabricated by Dean. As the rod runs a dry sump, this necessitated the separate oil tank, which is neatly matched to the rear-mounted vertical fuel tank, and one of the more visually appealing parts of the build, especially polished up and bristling with anodised connectors. Dean bent the rounded top end over a former, then cut and shaped all the other pieces of each tank to fit, before sending them off to Pat at Racecraft for welding. Being a TIG welder of excellent quality, who's done work for the likes of the DJR and Stone Brothers V8 teams in the past, Pat did as superb a job with these components as he did with the front suspension. While Pat was welding, Dean was purchasing a factory-spec polisher to buff the stainless to a mirror finish. While the industrial unit was used for items like the tanks, Dean hand-polished the firewall, which was custom built from aluminium sheet. The inlet and exhaust system was also all hand fabricated and mandrel bent, using 3 ½ inch pipes, which widen to 5 inch at the billet clamps for the muffler. Exhaust tip is an Invidia item.
While Dean was working on the running gear, his father took on the job of cleaning up and painting the body. Being a retired panel beater and spray painter, he had the skills for the job. As it turned out, he needed them, as the fibreglass body was pretty rough - maybe that's why it was only $200!
After spending time getting the 'glass smoothed and trimmed, it was time for paint. Dean had wanted a smoked silver metallic finish, but his dad convinced him to go with a warmer, champagne colour from the Mercedes paint chart. As it turned out, he was right; the soft gold shade is a good match to the black chassis and polished stainless steel. You may have noticed there are no doors on the bucket-style body. Dean told us he could have added them, but cutting the doors and fitting hinges, latches and rubbers meant more time and more cost on a build that already was taking up a lot of time and costing a lot of money. Being 6'2" Dean has no problem stepping into the car, but he cleverly added a pair of external side steps to make entry and exit easier for others. Those steps were actually cut from an old bulbar. On a trip to the tip, Dean saw the abandoned bulbar and thought the dimension of the tubing was ideal for a set of side steps, so he took it home with him!
Inside, Dean's bucket is quite spartan, with simple lap belts on a basic bench seat. The cluster of Auto Meter gauges featured more of Dean's fabrication work, with the speedo, dual oil pressure and water temp gauges all nestled in custom holders, joined by custom brackets, with more of those braided lines and anodised connectors. Nestled out of sight under the dash are the MSD ignition coils, which are mounted inboard of the firewall. What is noticeable in the cabin is the ribbed box in the passenger footwell, which is a watertight container that holds the engine computer and CDi system. In addition to making it watertight, Dean added provision to plug in a laptop to tune the engine, which he gets Matty Spry from P.I.T.S. (Performance Injection Tuning Services) in Molendinar to work his magic on.
With most of the project completed by 2007, there remained one major part that still hadn't been finalised - the wheels. Dean liked the look of the big five-spoke wheels on the BMW X5, but couldn't find an aftermarket style to suit - especially in the different sizes he was after (22x11" rear and 19x10" front) to create the hot rod 'bigs and littles' look. Dean's local Bob Jane T-Mart suggested Advanti's 'Gauntlet' five spoke wheel. Initially, Dean wasn't convinced and his son even less so, telling him those wheels would look horrible! But Dean at least allowed a set to be put on the Yokohama low profile rubber he'd ordered to see what they looked like. As it turned out, the T-Mart was right; the dished black rims with their machined faces looked the goods and suited the overall 'modern' look to the hot rod. When he saw them, Dean's son was convinced, too!
Finally, seven years after the project started, Dean's hot rod was complete. With the attention to detail and level of engineering, it's little surprise the car was not only quick, but handled as well. How quick?
Try 0 to 100 kph in about 3 seconds. It can also sprint to 160 kph faster than an R1 motorbike, which Dean has put to the test - on the racetrack of course!
Dean puts the cost of the project in the low six figures, and that only covers parts. But Dean loves it, and living on the Gold Coast, cruising in a roadster like this is about as good as it gets. Dean told us it's smooth to drive, reliable and excellent on fuel, too. Proof of the reliability of the vehicle is the fact it's covered more than 10,000 km since completion, including trips to Byron Bay and the Sunshine Coast.
Whether on the road or at a show, the rod always turns heads and attracts comments. It's picked up a few trophies as well. As you might expect, a few of the 'old school' rodders aren't fans, but plenty more love it and applaud Dean not only for doing something different, but doing it well. Dean told us that when he's cruising around the Gold Coast, he even gets Japanese tourists swarming over it and taking photos.
While Dean did approach this build as his 'only' project, the bug must have bitten, as he told us that he's already started another hot rod build - but this time with a roof! As good as the Gold Coast weather is, it still rains, and in a car like this, when it rains, you get wet. Dean's next project is a '32 Ford 5-window coupe with a Jaguar six-cylinder engine, transmission and diff. With memories still fresh from his debut build, Dean said he's determined to keep this one simple - and not spend seven years on it!
All images courtesy of www.dragphotos.com.au
Dean's 1923 T-bucket hot rod - basic specs
Engine: Nissan 300ZX V6 with o-ringed block and forged internals, GT42R Garrett turbo, twin 48mm wastegates, PWR intercooler, 4 stage Peterson dry sump system, 1000hp Magna Fuel fuel system, 1000cc injectors
Transmission: Nissan 300ZX 5 speed, 5 plate Nismo clutch, chromoly flywheel
Diff: Nissan 300ZX, viscous LSD, 3.9 ratio
Engine management: Autronic SM4 computer, R500 CDI ignition, MSD coils
Power: 400 RWHP @ 18lb boost
Brakes: Nissan 300ZX
Wheels: Advanti Gauntlet 5-spoke - 19" x 10" front and 22" x 11" rear
Tyres: Yokohama Advan Sport - 245/35 ZR19 front and 315/30 ZR22 rear
Build time: 7 years
Build cost:$125,000+
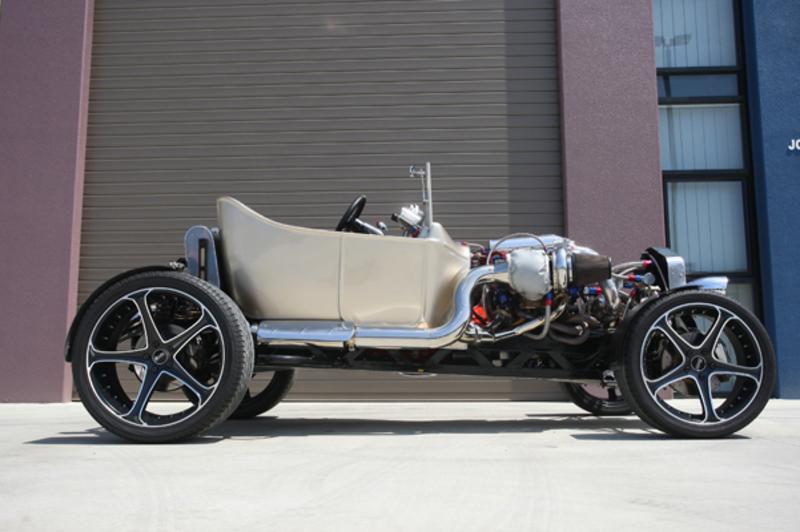
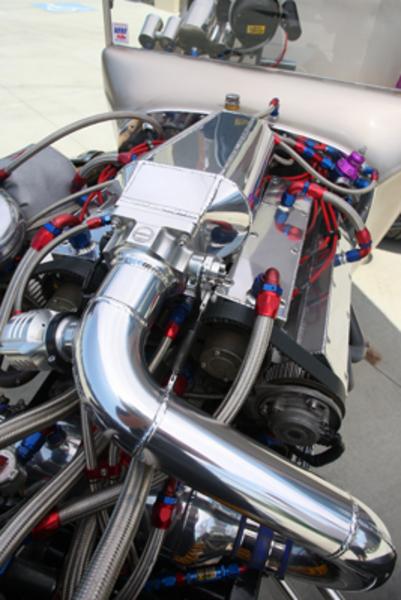
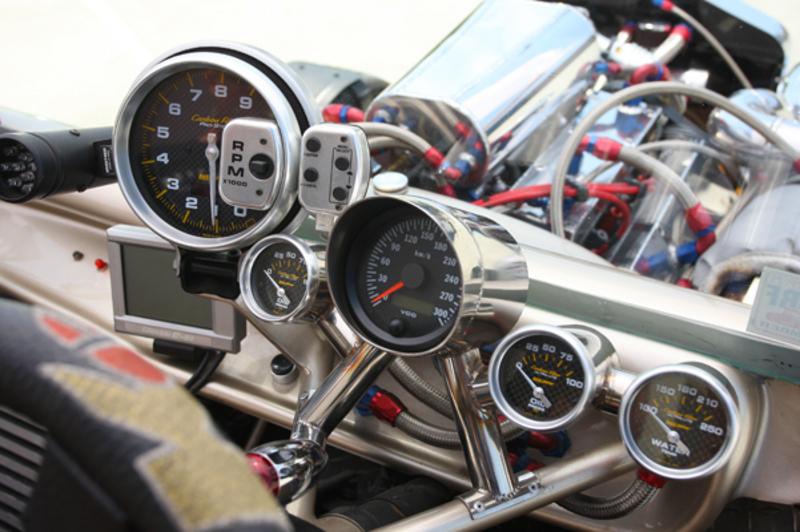
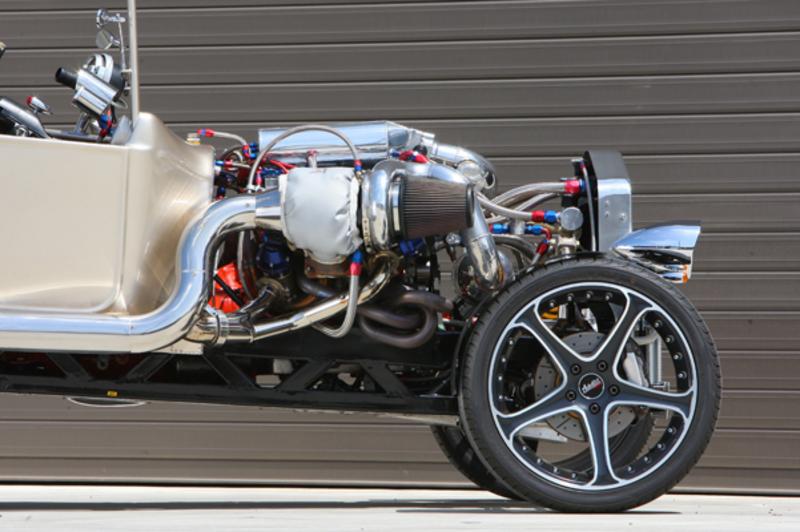
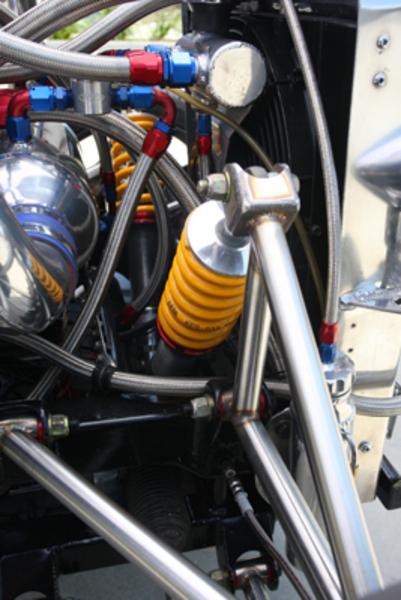
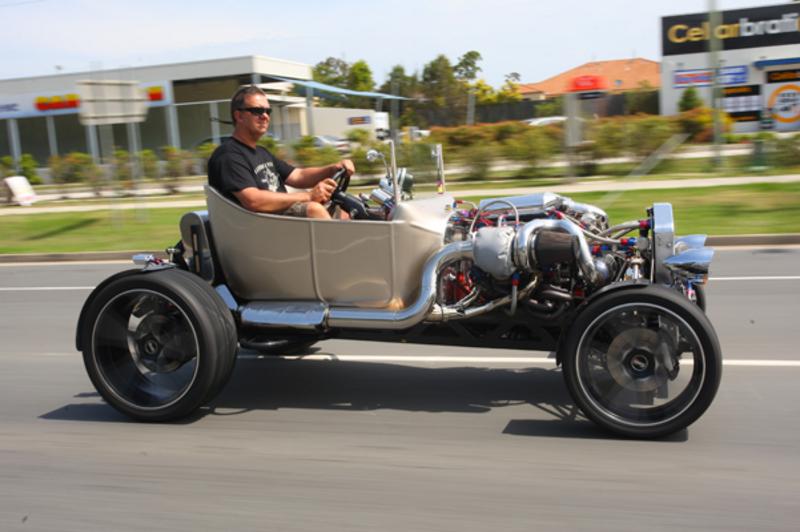
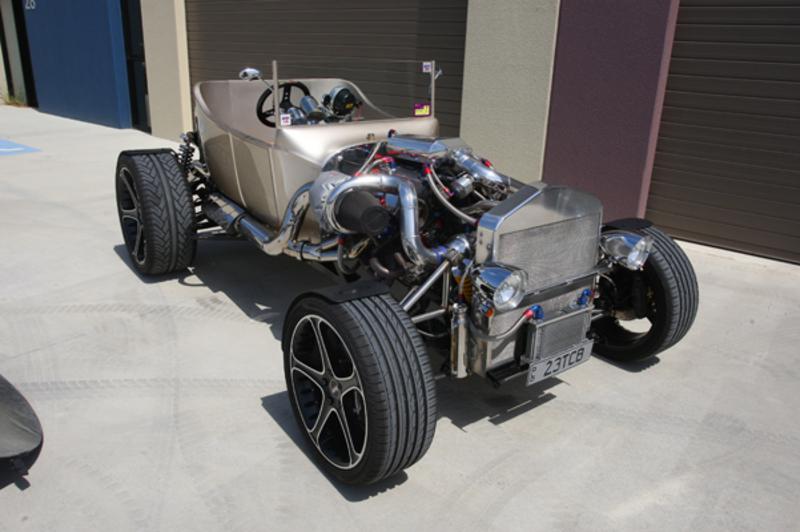
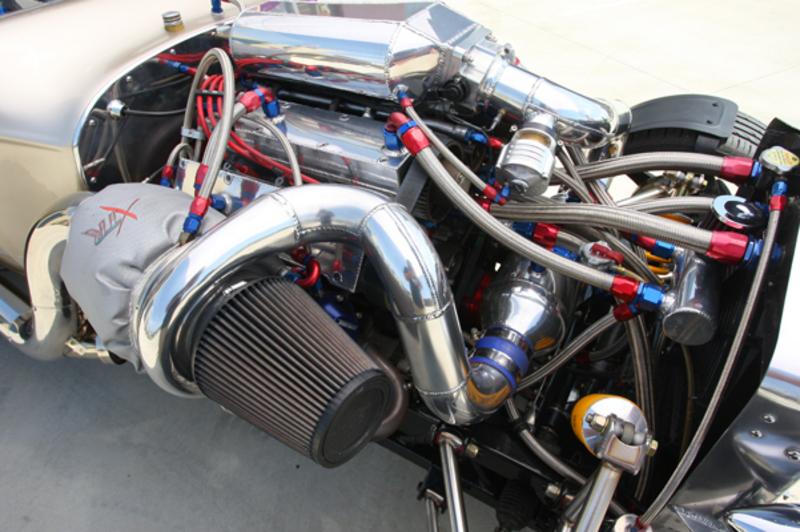
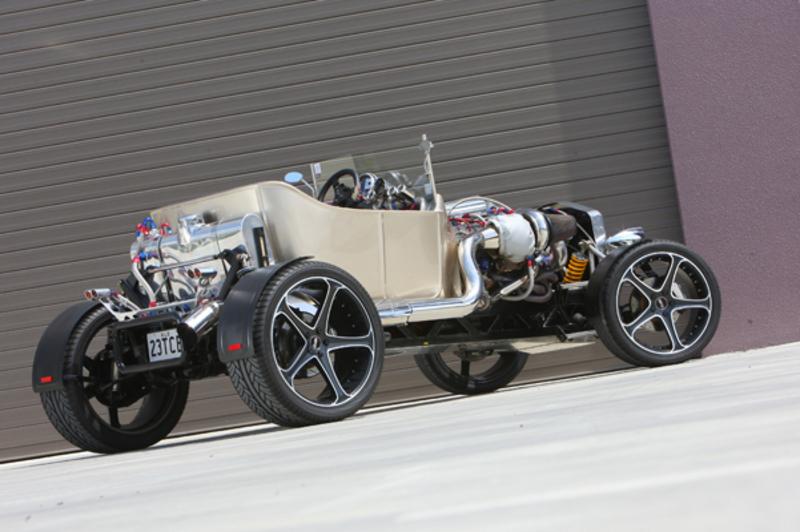
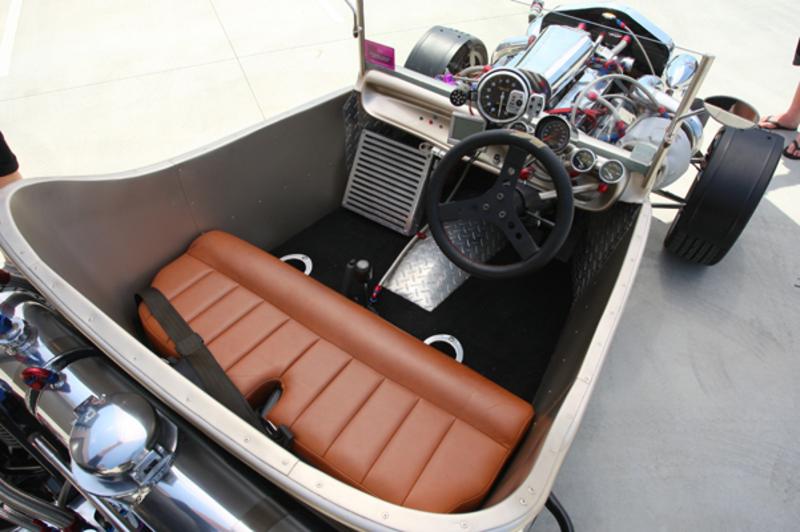
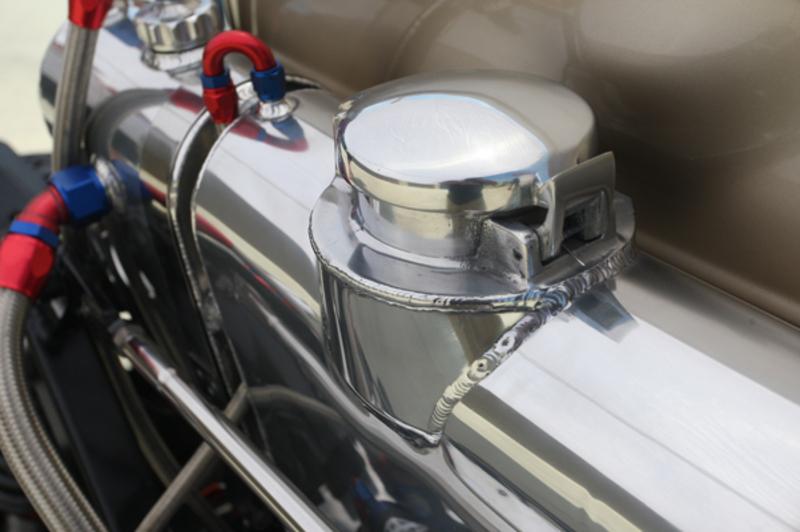